In der Materialflussbranche wird, wie in den meisten anderen Industriezweigen, viel darüber gesprochen, wie man die Produktivität optimieren kann. Die Produktivität lässt sich berechnen, indem man den Output, z. B. die Produktionsmenge oder die bearbeiteten Vorgänge, durch den Input bzw. die Einsatzmenge teilt. Stellt ein Betrieb also 12 Stapler während einer 8 Stunden Schicht her, so liegt die Produktivität bei 1,5 Stapler pro Stunde. Um die Produktivität zu erhöhen, muss ein Unternehmen also entweder den Output steigern oder den Input reduzieren. Dabei werden viele Einflussfaktoren mitberücksichtigt, allerdings wird der Staplerfahrer in der Intralogistik als eine wichtige Einflussgröße häufig vergessen. Ein Staplerfahrer, der sich wohlfühlt, kann effizienter arbeiten, was sich positiv auf die Produktivität auswirkt.
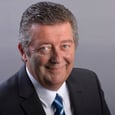
Dieter Schorn
Aktuelle Einträge
Wie Ergonomie sowohl Staplerfahrern als auch den Logistikbetrieben zugutekommt.
Intralogistikexperten – so meistert Skechers seinen herausfordernden Materialumschlag.
Skechers ist einer der größten Produzenten von Sportschuhen weltweit. Das aus den USA stammende Unternehmen ist nicht nur in seinem Heimatland äußerst erfolgreich, sondern auch in Europa. Dieser Siegeszug wird durch die enorme Größe des europäischen Distributionszentrums (EDC) der Firma in Lüttich, Belgien, unterstrichen. Auf 118.000 m2 Fläche sind rund 75 Lagertechnikgeräte im Einsatz, deren Aufgabengebiet vom Be- und Entladen der LKWs über die Versorgung des Hochregallagers und die Kommissionierung der Waren bis hin zur Versandvorbereitung reicht. Bis zu 3.500 Kundenaufträge werden täglich im EDC bearbeitet. Insbesondere vor dem Hintergrund, dass circa 40% des gesamten Jahresvolumens allein in den ersten drei Monaten eines Jahres umgeschlagen werden, stellt sich die Frage, wie ein solch effizienter und optimierter Materialfluss in der Praxis aussehen kann.
Wie Sie ihr Warenlager sicherer und produktiver gestalten.
Die richtige Wahl eines Staplers wirkt sich positiv auf die Arbeitssicherheit aus. Ist dieser ergonomisch designt, so werden körperliche Belastungen von Fahrern verringert, wodurch Überlastungsverletzungen vorgebeugt werden können. Doch ist der passende Stapler nur ein Puzzleteil, das für eine optimale Arbeitssicherheit benötigt wird. Die Konzeption des Lagergebäudes trägt ebenfalls ihren Teil dazu bei.
Kosten und Nutzen im Vergleich – wann Sie Ihren Stapler behalten und wann Sie ihn ersetzen sollten.
Unabhängig von der Qualität eines Staplers, nimmt dessen Leistung nach einigen Jahren in einem geschäftigen und schnelllebigen Betrieb ab. Die Produktivität und Effizienz des Warenumschlags können durch Stapler, die schon länger im Einsatz sind, erheblich sinken, weswegen der Zeitpunkt diese zu ersetzen unausweichlich kommt. Aber wie kann man feststellen, ob ein Stapler nach wie vor die gewünschte Leistung erbringt bzw. wann der Zeitpunkt gekommen ist ihn aus dem Verkehr zu ziehen? Welche Möglichkeiten gibt es diesen zu ersetzen oder optimal einzusetzen? Das obenstehende Diagramm veranschaulicht Ihre Möglichkeiten und wann welche Option berücksichtigt werden sollte.
Ein effizienter Materialfluss gelingt nur mit den passenden Staplern
Der Vorgang des Be- und Entladens von Waren kann auf verschiedene Arten durchgeführt werden. Je nach Prozessablauf und Aufbau des Lagers kann eine bestimmte Methode wesentlich effektiver sein als eine andere. Beispielsweise können Waren mithilfe eines Elektro-Niederhubwagens schneller mit Fahrerstandplattform ein- bzw. ausgeladen werden als ohne Plattform, insbesondere wenn längere Strecken zurückgelegt werden müssen. Der anspruchsvolle und kostspielige Prozess der Kommissionierung bietet sogar noch mehr Möglichkeiten zur Optimierung. Was können Sie jedoch für den dritten wesentlichen Bestandteil der Materialförderung – die Einlagerung und Entnahme ganzer Ladeeinheiten innerhalb des Warenlagers – tun, um die Effizienz und Produktivität zu steigern?
Sicherer, ergonomischer und daher effizienter Materialumschlag bei Skechers
Täglich bis zu 3.500 Kundenaufträge, 118.000 m2 Lagerfläche, rasantes Wachstum – der Materialumschlag der Marke Skechers stellt eine Herausforderung dar, insbesondere wenn man bedenkt, dass rund 40 Prozent des gesamten Jahresvolumens des Schuhherstellers in den ersten drei Monaten eines Jahres umgeschlagen werden. Um dem Auftragsvolumen gerecht zu werden, wird das europäische Zentrallager des Unternehmens in zwei Schichten betrieben. Jedoch muss jedes Zahnrad dieses komplexen Prozesses ineinandergreifen. Ausfallzeiten der Staplerfahrer, die aus Verletzungen auf Grund von permanenter körperlicher Belastung resultieren, oder Auffahrunfälle verringern die Produktivität des Materialumschlags enorm. Die eingesetzten Flurförderzeuge sollten daher auf die Fahrer angepasst und ergonomisch konstruiert sein. Doch inwieweit berücksichtigt Skechers diese Themen für die eigene Staplerflotte?
Wie Sie Ihre Betriebskosten in schwierigen Zeiten senken
Der Kampf, unnötige Kosten auf ein Minimum zu beschränken, ist für Fachleute der Materialhandhabung immer ein wichtiges Thema. Aber wenn sich wirtschaftliche Entwicklung abflacht und der Geschäftsbetrieb gestört wird, wie während der aktuellen COVID-19-Krise, wird der effiziente Einsatz Ihrer Ressourcen noch bedeutender. Viele Logistikunternehmen versuchen, Geld zu sparen, indem sie sich für billigere Flurförderzeuge entscheiden oder unnötige Ausgaben wie Schulungsmaßnahmen reduzieren. Einsparungen in diesen Bereichen können zweifellos Ihre Kosten reduzieren, allerdings spielen diese Kosten nur eine untergeordnete Rolle im Vergleich zu den größten staplerbezogenen Kosten, die den Staplerfahrern zugeschrieben werden.
Reibungsloser Flottenbetrieb – die Modernisierung der Staplerflotte von Helly Hansen
Da der norwegische Bekleidungshersteller Helly Hansen ein stetiges Wachstum verzeichnen konnte, musste das Unternehmen den Standort seines europäischen Distributionszentrums wechseln. Das neue, 20.000 m2 umfassende Distributionslager im südniederländischen Born verfügt über circa 60.000 Stellplätze und beherbergt 24.000 Bestandsartikel. Insgesamt befinden sich ungefähr 2,5 Millionen Artikel auf Lager. Die logistische Abwicklung dieser Vielzahl an Waren erfordert nicht nur eine leistungsstarke und anforderungsgerecht gestaltete Staplerflotte, sondern auch die Anwesenheit eines zuverlässigen Partners an seiner Seite. Diesen hat Helly Hansen in Logisnext (vormals UniCarriers) gefunden und sich bei der Modernisierung der Flotte auch an diesen gewandt.
Wie wirkt sich ein ergonomisch designter Staplermast auf die Lagereffizienz aus?
Bis zu 70 Prozent der Gesamtbetriebskosten eines Staplers entfallen über seine gesamte Lebensdauer auf den Staplerfahrer. Deshalb sollte der Fahrer an sich betrachtet werden, wenn Sie Ihre Kosten minimieren möchten. Hierbei spielt das Thema Ergonomie eine entscheidende Rolle, denn von einer gesteigerten Ergonomie profitiert nicht nur die Gesundheit des Staplerfahrers, sondern auch die Effizienz, Produktivität und Sicherheit Ihres Materialumschlags. Eine Studie der Chalmers University of Technology in Göteborg hat in Zusammenarbeit mit der UniCarriers Group aufgezeigt, dass ein Staplerfahrer mehr als 1.000-mal in der Stunde den Kopf dreht. Eine gute Rundumsicht, insbesondere ein ergonomisches Mastdesign, ist daher von großem Nutzen und kann die Anzahl der Kopfbewegungen reduzieren und damit auch die körperliche Belastung für Nacken und Rücken verringern.
Sportliche Höchstleistungen beim Materialumschlag
„40 Prozent unseres gesamten Jahresvolumens schlagen wir allein in den ersten drei Monaten um.“ Das sagt Bart Geenen, Director of Operations des europäischen Distributionszentrums des amerikanischen Schuhherstellers Skechers. Die neuen Schuhkollektionen treffen in den Monaten Januar bis März, aber auch von Juni bis August ein. Aus diesem Grund herrscht zu diesen Zeiten Hochbetrieb im Distributionszentrum und Skechers benötigt mehr Stapler als sonst. Doch wie geht das Unternehmen mit solchen Umschlagspitzen um?